MANUFACTURING FACILITIES
Since December 2015 we are operating at our new 60,000 sq. ft. manufacturing facility established Plot No. C-1/B-1/A-9,GIDC Phase – 1,BHARUCH Gujarat – 392 001 at a cost of US$2.5 Million (Rs. 120 Million). This new factory is located approx. 150 km from the international port and airport at Mumbai. This factory has two manufacturing bays 56m long x 20m span capable of handling large vessels and skids up to 50 tons weight. Latest Welding equipments, rotators, manipulators, OH Cranes, Shot blast room, Paint booths, 500KVA power with full back-up generators are available to manufacture products that meet international quality standards at a competitive price and timely delivery. This facility is ASME “U”, “U2”, “S”, & “PP” certified permitting us to manufacture coded pressure vessels, Power Boiler Equipment and power piping.
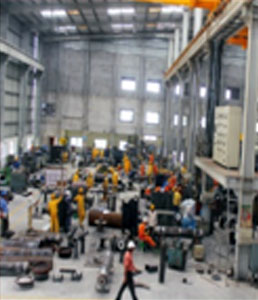
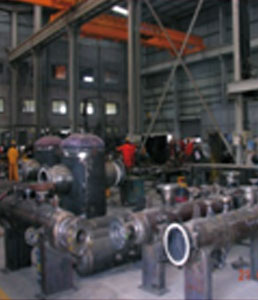
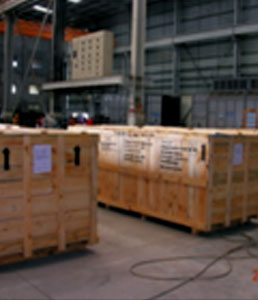
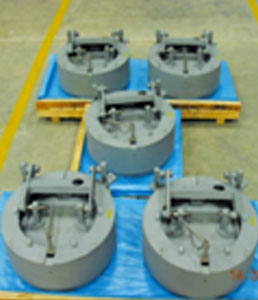
DESIGN
Our company has over the years, developed total engineering capability in the core competency areas of liquid & gas filtering/metering. Products are manufactured under an ISO : 9001-2008 quality system. Constant product innovation ensures that we keep pace with the ever increasing accuracy demands from flow metering systems. Latest design software ”PV ELITE-2012″ is used for pressure vessel & heat exchanger design to ASME BPV code section VIII Div 1 & 2, European Norm EN 13445, British standard BS 5500 and Australian Standard AS-1210. Finite element (FE) analysis by ANSYS & 3-D solid modeling is used to design and analyze highly stressed parts like Quick Opening Closures & nozzles.


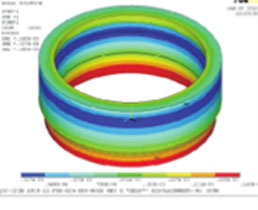
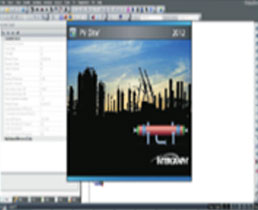
PRODUCT FINISH, SURFACE TREATMENT & COATING
We strongly believe that a finely engineered product, manufactured & tested to the high demands of the Oil & Gas industry, deserves a surface coating of unsurpassed reliability to withstand the rigors of the extremely harsh environments in which they are designed to be installed : Deserts with sand storms, saline sprayed offshore platforms, frigid arctic zones & steamy tropical jungles. The coating application has to be nothing less than perfect and we take this very seriously indeed. Our factory has world class shot blasting and paint application facilities. Our coating procedures and applicators are qualified by NACE level 2 certified coating inspectors. Every process is rigorously checked to achieve perfection

Coating adhesion strength by dolly pull down method
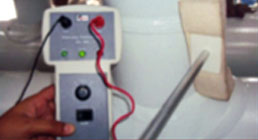
Holiday test of protective non-conductive coating on metallic surface
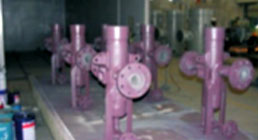
Strainers emerging from shot blast
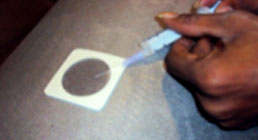
Measuring salt level content on metal surface after shot blasting
PRODUCT TESTING & DEVELOPMENT
All our products have been developed in-house. Our finger are constantly reading the pulse of our customer’s expectations from our products and comparing this with our actual product performance in the field . This tells us when need to improve and innovate. Continuous product testing , on field/at testing labs ensures that we meet the committed product performance efficiencies. Our entire range of liquid stainers has been pressure drop checked at external test labs for flow rates up to 3000m3/hr. Our own Flow testing facility is being set up the Chakan plant. We have successfully developed. manufactured and commissioned Quick Opening Closures (QOC’s) for liquid /gas filters of sizes up to 32” CL. 900/58” CL. 300/64”CL150. Our zeal for providing quick solutions for difficult problems has resulted in the development of automatic air vents for high pressure applications (up to 200 bar). We are one of the few in the world who have successfully built air vent valves for these pressures. All vessel internals like Axial & Tangential Multi Cyclones, Vane Demister Packs & Schoepentoeters are designed & manufactured in-house. Computational Fluid Dynamics (CFD) & Modeling is used for design optimisation for different applications.

UT thickness checking
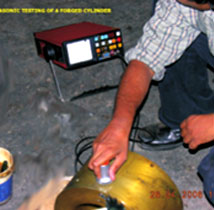
UT On Forgings

32" fabricated strainer on pressure drop testing at CWPRS
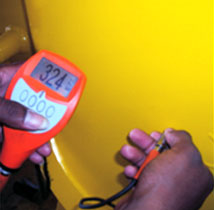